Abstract
This review aims to explore the diverse facets of pesticide A.I.s incompatibility, providing real-world examples of incompatible combinations and clarifying the underlying chemical interactions that govern such phenomena. By gaining a thorough understanding of these complexities, we can pave the way for the development of more effective and environmentally responsible pesticide formulations.
The author proposes to help in identifying, investigating, and resolving A.I.’s incompatibility issues in pesticide formulations, contact the author.
Introduction: Pesticide formulations often employ a synergistic combination of active ingredients (A.I.s) to broaden their spectrum of pest control. However, the critical importance of ensuring the compatibility of these A.I.s cannot be overstated, as it directly affects the desired outcomes. Incompatibility among pesticide A.I.s can lead to a variety of problems, including reduced effectiveness, physical precipitation, the formation of toxic compounds, and potential hazards to human health and the environment.
During the development and practical application of each formulation, it is critical to address two fundamental aspects of incompatibility challenges.
First, incompatibility issues frequently manifest during the field application of these formulations in tank mixes.
Second, achieving a harmonious blend of multiple A.I.s into a single composition is always a recurring and significant challenge. In the article, the following matters are considered:
- Incompatible formulations in tank mix
- Evaluating the potential compatibility of tank mix partners
- Chemical Incompatibility of Active Ingredients combined in single formulation
- Complexation of Pesticide Molecules with Metal Ions and Free Metals
- New formulation development. A compatibility-centered approach
- What to do when the incompatibility issues manifested in ready formulation?
The article presents some available published data on chemical incompatibility in tank mixes and between active ingredients combined in a single formulation. It also explores potential scenarios for problem-solving.
1. Incompatible formulations in tank mix: Tank mixing involves the process of combining various crop protection products into one tank, enabling a single application for multiple products. While this method proves convenient and time-efficient, it is essential to carefully assess the compatibility of the mixed products in the field. In practice, there is often some form of interaction between the molecules of the combined products, with outcomes ranging from additive to antagonistic or synergistic effects. Below, we present examples of published data illustrating incompatible combinations of different formulations.
Incompatible formulation mixtures A + B
It's important to note that the examples mentioned above serve solely for informational purposes and may not encompass all potential chemical incompatibilities.
In addition, several other variables can significantly influence the compatibility of CPPs in a tank mix, potentially resulting in adverse effects:
- High pH: In most cases, up to 90% of the spray solution consists of water, and many pesticides are sensitive to high pH levels. A high pH can cause hydrolysis of certain pesticides, reducing their effectiveness. Moreover, it can decrease the solubility of specific pesticides.
- Water Hardness: Water with a high concentration of dissolved minerals can react with sensitive pesticides, leading to decreased efficacy (e.g., glyphosate, 2,4-D).
- Addition of Fertilizers: When fertilizers are added to crop protection products in a tank mix, their compatibility can be adversely affected for several reasons: there may be chemical reactions between the fertilizers and some of the active ingredients, leading to altered efficacy; the pH effect of the fertilizers can shift the pH away from the optimum range for the crop protection products, potentially reducing their performance; formulation issues may arise, as crop protection products are designed to work effectively within specific conditions, and the addition of fertilizers may disrupt this balance; there is a risk of crop safety, as the combination of fertilizers with CPPs can cause phytotoxicity,
- Low Temperature: Low temperatures can reduce the solubilization and dispersibility of products causing separation or sedimentation of the tank mix partners.
- Mixing Incompatible Formulation Types: Oil- and water-based pesticides do not naturally stay mixed. Wettable powder (WP) and emulsifiable concentrate (EC) formulations contain different surfactants and carriers. Mixing these formulation types can cause emulsion destabilization or separation, leading to poor application quality and reduced efficacy. It is advisable to apply them separately or seek compatibility information from the pesticide manufacturer.
-
Mixing Order: When combining pesticide formulations with varying mixing characteristics, it is essential to follow the WAMLEGS mixing acronym. WAMLEGS stands for:
W – Wettable Powders
A – Agitation (anti-foaming agents and buffers)
M – Microencapsulated suspension products
L – Liquid and soluble products
E – Emulsified concentrates
G – High-load glyphosate products
S – Surfactants
After completing the sequence, micronutrients and other fertilizers can be added. Mixing them in the wrong order can lead to problems. For instance, altering the mixing order by adding dry formulations or water-soluble bags after emulsified concentrates can result in a phenomenon known as "wrapping" of the dry or bag material. This means that the emulsifier will surround the dry particles or water-soluble bags, preventing them from dissolving properly. To avoid such complications, it is advisable to create a pre-slurry with dry formulations and water-soluble bags first.
- Insufficient Amount of Spray Solution Water: The quantity of water that is used to prepare a tank mix is crucial. Mixing instructions usually recommend filling the tank halfway with water first. If an inadequate amount of water is used, the tank mix partners will not fully solubilize because the solution becomes saturated. Likewise, you could have mixing issues if you begin adding actives when the tank is less than 20% full.
2. Evaluating the potential compatibility of tank mix partners: Practically, to determine the compatibility of products, conducting a jar test is crucial. When performing the jar test, it is essential to use the current product intended for the tank mix, avoiding any leftovers from previous years. Chemical formulations may have been updated, and using outdated samples can yield inaccurate results. Additionally, ensure that the water used for the jar test matches the water used as the carrier for the spray solution. This consistency is essential as different water sources can influence compatibility. Lastly, add the tank mix partners to the jar in the same ratio as you would for the actual spray tank. Following the recommended jar test guidelines provided on pesticide labels will offer more specific information and ensure accurate results.
Jar test:
- Take a glass jar and wash it properly.
- Add 500ml of water into jar.
- Add pesticides in proportion to the rate to be used in the field.
- Then, cap the jar and shake it well.
- Leave the jar stand undisturbed for overnight.
- If both pesticides are mixed properly without leaving any sign of incompatibility, then it is good for making mixture in tank for spray.
- If a separate oily layer, large agglomerate of granules, gel, clumps of solids or sludge forms in the bottom of jar, the mixture is incompatible.
3. Chemical incompatibility of Active Ingredients combined in single formulation: Chemical incompatibility can arise when one or more mixing partners undergo chemical reactions with each other. Ensure successful mixes, it is advisable to utilize pesticide compatibility charts provided by reputable universities and extension services. Additionally, when dealing with unfamiliar or complex tank mixes, always conduct jar tests to assess compatibility accurately. One of the published pesticide incompatibility charts is provided in the attached file, which presents example of available data.
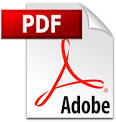
It is essential to emphasize that blank cells in the provided table indicate a lack of data on certain combinations. In cases where there is no available information, any attempt to mix these components in one formulation should undergo thorough investigation and evaluation. Prior to combining such untested combinations, it is crucial to conduct extensive research and analysis to ensure compatibility and avoid any potential risks or adverse effects.
Some examples of possible reasons for the chemical incompatibility of active ingredients (A.I.s) in mixed formulations can be attributed to the following:
- Combining alkaline pesticide formulations, like lime sulfur, with acidic products, such as certain herbicides or growth regulators, can trigger chemical reactions that degrade the active ingredients.
- Interactions between organophosphate insecticides, such as malathion, can undergo chemical reactions when mixed with copper-based fungicides like Bordeaux mixture resulting in the formation of insoluble precipitates, reducing the effectiveness of both pesticides.
It is recommended to avoid mixing such pesticides.
4. Complexation of Pesticide Molecules with Metal Ions and Free Metals: In numerous instances, the chemical incompatibility of active ingredients can be attributed to the inherent ability of pesticide molecules to form stable complexes with metal ions present in the tank mix or within the formulation. This phenomenon arises from the chemical interactions between the pesticide molecules and metal ions derived from another molecule or introduced inerts. Consequently, such a complexation events profoundly influence the bioavailability and potential toxicity of the pesticide formulation. Several examples of complexation include:
-
Complexation of Atrazine with metal ions: 2-chloro-N4-N6-isopropyl-1,3,5-trizine-4,6-diamine, or Atrazine,
can form complexes with different metal ions with theformula [M(Atr)n.xH2O.yCl] where M = Mn, Fe, Co, Ni, Cu or Zn; n = 1 or 2; x = 1–4; y = 1–2. Such metal to atrazine complexes often incorporate coordinated water molecules to the metal ions within the complexes. These complexes exhibit diverse structures, comprising one or two atrazine molecules with one metal ion, along with varying numbers of water and chloride ions. Manganese (Mn) and copper (Cu) form 1:2 complexes, where coordination takes place through the nitrogen of the ring. Iron (Fe), cobalt (Co), nickel (Ni), and zinc (Zn) ions form a 1:1 complex, involving both the nitrogen of the ring and the nitrogen of NH in the coordination process.
-
Complexation of carbamates and organophosphates with transition metal ions (Mn2+, Fe3+, Co2+, Ni2+, Cu2+, and Zn2+): The carbamates and organophosphate molecules (A - organophosphates, B – carbamates), form quick and stable complexes with transition metal ions:
These complexes are insoluble in water at almost all pH, their transfer to plant/animal body is therefore not possible.
5. New formulation development. A compatibility-centered approach: Considering the foregoing, it becomes evident that the development of a new formulation necessitates the implementation of a compatibility-focused approach. Central to such an approach is the meticulous consideration of two main aspects pertaining to incompatibility challenges.
Firstly, the successful combination of several A.I.s into a single composition is crucial.
Secondly, it is essential to ensure the new formulation's effective application under various local conditions. This includes considering different possibilities of tank-mixing with other CPPs, adjuvants, and fertilizers, accounting for specific weather conditions, sources of spraying water, its amount, temperature, and hardness at each application site.
To achieve success, formulators must have access to key information concerning the future field application of the formulation. This includes the type of application, minimum and maximum amounts of spraying water, its temperature and hardness, as well as the minimum and maximum application rates of the formulation. Additionally, knowing potential partners for tank mixing is crucial. All these essential data should be provided in a comprehensive technical design specification, outlining the requirements, specifications, and objectives for the development of the new formulation. Such a document serves as a guiding resource for the formulators' team, enabling them to develop the project according to the customer's specific needs and expectations.
The availability of detailed information about field application conditions, which can vary significantly across different localities, empowers the formulators' team to make informed decisions. With comprehensive data in hand, they can choose the optimal formulation type and select suitable inerts for the new composition. The team can then conduct necessary jar testing in various water sources with different temperatures and hardness levels, as well as experiment with combining the prototype formulation with various tank mix partners. Furthermore, simulation testing in the spraying tank, using different types of nozzles under different conditions, becomes a valuable practice in the formulation development process.
Embracing a compatibility-focused approach and possessing extensive information about field application conditions enhance the formulators' chances of success in developing a new formulation. The thorough testing and strategic decision-making throughout the development process ensure a robust and effective product ready for real-world applications.
6. What to do when the incompatibility issues manifested in ready formulation? In the context of resolving incompatibility problems in pesticide formulations, it is crucial to distinguish between issues arising during the application of the formulation in a tank mix and those originating within the formulation itself during storage or production. To address such problems effectively, a systematic approach is required.
When encountering customer complaints related to incompatibility, the first step is to gather comprehensive information. The primary question to be answered is whether the problem occurred in the formulation or the tank mix. This determination will dictate the subsequent actions.
Tank mix incompatibility
For tank mix incompatibility problems, the following strategy can be adopted, contingent upon the identified reasons for the issue:
High pH: Perform a Jar Test for the formulation or tank mixture, incorporating various pH adjusters, buffers, water conditioners with multiple modes of action available in the market. The aim is to recommend suitable additives to the customer for the tank mix or to provide them along with the formulation.
Water Hardness: Like the previous step, conduct Jar Tests with the addition of various softeners or "compatibility agents" to the tank mix. Identify a suitable agent and recommend its use or supply it together with the formulation.
Addition of Fertilizers: Conduct a Jar Test with the addition of fertilizers used by the customer. If the problem is confirmed to be caused by the mixture, advise the customer to avoid using such combinations and include this information in the product label instructions.
Low Temperature: Perform Jar Tests at various temperatures to determine the optimal temperature range for tank mix application. Include this information in the product label instructions.
Mixing Incompatible Formulation Types: Utilize available pesticide compatibility charts provided by universities and extension services. Always perform Jar Tests for unfamiliar or complex tank mixes. If the formulation is found to be incompatible with another one applied by the customer, instruct them to avoid such mixing, and include this information in the product label instructions.
Mixing Order: Conduct Jar Tests with the same mixtures used by the customer to identify the proper mixing order. Instruct the customer accordingly and include this information in the product label instructions.
In conclusion, if any of the reasons mentioned above for tank mix incompatibility are identified and addressed, it is essential to reflect these findings on the product label. Failure to address these issues during product development must be considered for future improvement.
Formulation with built-in incompatibility issues
For scenarios involving inherent incompatibility problems within the formulation itself, a thorough investigation is imperative. The course of fixing actions will hinge upon the discoveries made during this investigation:
Chemical reaction between A.I. molecules: If it is confirmed that molecules of different active ingredients in the formulation react with each other, one potential solution is to separate the active ingredients. This could involve encapsulating one of the A.I.s or considering a formulation type change (e.g., from water-based to oil-based, or from SC to SE) to prevent chemical interactions. The possibility of using solid formulations instead of liquids should also be explored. Before reformulating, a thorough investigation of the chemical interaction and its mechanism is essential to find an appropriate solution.
Chemical reaction between A.I. molecule and inert additive: If an interaction between an active ingredient and an inert additive is detected, replacing the incompatible inert agent with a suitable alternative is a viable option. For instance, if Urea (applied as anti-freezing agent) reacts with an A.I., it can be replaced with glycol.
Complexation of A.I. molecule with metal ions: In cases where A.I. molecules form complex with metal ions, identifying the source of the ions and reformulating the formulation without components containing such ions is necessary.
Changes in A.I. molecule due to hydrolysis, pH change in storage: If hydrolysis or pH changes in the formulation lead to incompatibility issues, the root cause must be investigated. The findings of the investigation can potentially lead to the discovery of an appropriate solution.
In conclusion, resolving incompatibility problems manifesting within the ready formulation presents significant challenges. A thorough investigation into the root cause is essential to identify appropriate fixing actions. Despite the complexities involved, there are often viable solutions to be found, making it crucial to pursue this process diligently.
Conclusion: The comprehension of pesticide active ingredient incompatibility is paramount for ensuring their safe and efficient applications. Chemically incompatible A.I.s can lead to the formation of reactive products that diminish effectiveness and create significant challenges, rendering the use of CPPs impossible. Mixing pesticides with fertilizers may result in physical precipitation or chemical reactions, further complicating the situation. Additionally, the complexation of pesticide molecules with metal ions and free metals can decrease bioavailability and potentially induce toxicity. It is vital to recognize and effectively manage these incompatibilities to optimize pesticide utilization in agriculture and environmental management endeavors. By doing so, we can enhance the overall efficacy and sustainability of pesticide practices, minimizing risks to both human health and the environment.